Saturday, December 15, 2007
I'm Not Using a Sawzall Anymore!
Thursday, September 27, 2007
Another one for sale & more bodywork progress

Here's another chance to join me in my madness...there's another sedan for sale on eBay. It may not have as solid bodywork as the last one I posted did, but it sounds much better mechanically. I wonder why they took it off the road?
BTW, while I'm thinking about it, if anyone out there has a really nice trim piece for the fake hood scoop I'm interested. The one I have is quite pitted, but I'm not sure I'm willing to shell out $100 or more for the reproduction ones that appear from time to time on eBay.
If you're interested in the sedan, here' s the link to check the auction out:
As far as Chrissy (my car) goes, right now the nose, lower valence and two new panels I fabricated for between them are being held on by vice grips. I had to make a trip to Harbor Freight tools to get enough...but it's nice to see the car starting to look complete again. There is still some shaping work to do to make sure all the panels lineup but I hope to get to some of that this weekend. Once all trimming and tapping is done, I'll take the panels off one more time, protect everything I can with paint, reposition them back and start welding. That should take some time and I'll definitely need some help with holding part of the nose in the right place. I'm also going to be welding up the holes for the original nose badge as it won't be reinstalled. I've never really cared for it, and as the "TRIUMPH" letters will still be there I think that's ornamentation enough for now.
Sunday, September 09, 2007
Reconstruction at Last!
No, the welding is nothing pretty, but it is strong. I wanted to make sure that if the car was ever in an accident again, the front would hold up at least as well as it did when it was new. I'll be carrying my wife and daughter with me and I can't imagine more precious cargo.
Sunday, July 29, 2007
OH, what a deal....

I'm probably lucky this isn't in North Carolina...a RUST-FREE saloon just surfaced on eBay. At this point it's $300 no reserve. AAARRRGGGHHH!
Here's the link. Good luck to someone living near Oregon...
Having visited the hospital this week as a patient, I have no other news to report. I'm feeling fine now so hopefully there will be more progress this week... :-)
Jamie
Monday, July 16, 2007
Back to work with rusty metal...
I'm getting used to seeing old rusty metal at night. Here's to getting rid of it one way or another!
A NOS front lower valence...I just LOVE the old Stanpart label. Don't know if I can save it but I'll try...
A set of 7X15 wheels. Yeah, they're LOUD, but the color ought to work well with the cream paint and red interior. Thank heaven for the upsurge in AE86 Toyota drifters that have the same bolt circle and offset as TR's.... :-)

Yes, there's actually supposed to be sheetmetal there. Oooops. I only wish that the "craftsman" that did the previous work actually was one.
It's been a while since my last update. Here's some of the parts purchases:
So, where we last left the project I had to attack the nose. First, one half came off:
Which was enough to expose that there was a lot more work to be done. Then, the other half came off. That's the new nosecone below:
Unfortunately, I'll be creating some panels myself using the old cardboard and transfer method. You can see why here:
Yes, there's actually supposed to be sheetmetal there. Oooops. I only wish that the "craftsman" that did the previous work actually was one.
I'll try to update sooner. Maybe by the next post I'll be attaching rather than detaching!
Jamie
Thursday, April 26, 2007
It's been a while...
I'm shooting to have the car completed by November...that will be the 40th anniversary of it's delivery! With all new polyurethane bushings, the Stag anti-roll bar, new shocks and struts and 15" TR6 wheels, the car ought to feel pretty good on the road. The Stag front brakes (Ted Schumacher of TS Imports is rebuilding mine right now) should help keep it safe, along with the new seat belts.
Since my daughter Allyson will be spending a lot of time in the back seat, Cheri and I are currently considering installing a DVD player in the roof...I'll bet, if we do it, that it will be one of the very first times one's been installed in a 2000. BTW, although it's really not correct, I've started to refer to the car as the 2500, since that's really what it will end up being.
If you take another quick look at the photo at the top of this entry, the TR6 engine on the left hand side of the picture is what will power the car. As I recall (it was rebuilt over 10 years ago but has been turned over and kept oiled since) the engine was balanced, slight shaving of the head, 20 over pistons and a "stage 1" cam that was only slightly more aggressive than stock.
Enough for tonight. I hope to show real progress by the next entry!
Wednesday, March 07, 2007
Some welding repairs
These were actually taken before the priming, but I thought they were worth it from a contrast standpoint with my foolish attempts to weld the existing metal back together. Now, I have a real battery box...
The moisture is from coating the box with OSPHO...I'm using that stuff on the advice of someone that knows a lot more about this type of thing than I do.
It's SO nice to actually be putting parts on rather than taking them off!
The NOS valence came in, and it really is NOS, down to the Stanpart label! Only one major part to come by now...a manual driveshaft.
Tuesday, February 13, 2007
Wow! Some primer applied!!!
Over last weekend, finished the welding on the battery box and both sides of the front panel that the radiator bolts to...treated everything with Ospho and actually primed 3/4 of the engine compartment. Unreal, it's the first thing in a long time that I've done to the car that wasn't taking something off.
I'm hoping to take vacation again this Friday and will try to accomplish some more. I just won an auction on eBay for a NOS front valence, which as you can see from the pictures Chrissy needs pretty badly...
Gotta get her on the road!
Jamie
I'm hoping to take vacation again this Friday and will try to accomplish some more. I just won an auction on eBay for a NOS front valence, which as you can see from the pictures Chrissy needs pretty badly...
Gotta get her on the road!
Jamie
Friday, January 19, 2007
Pictures from recent work

Picture 1 shows the radiator support panel, now roughly straightened and welded back together, along with the back side of the "nosecone." You should also note the cut in the grille support thoughfully supplied by the previous "bodyman."
Picture 2 is a shot of the same area on the other side of the car from a more vertical angle. You can also see the holes left in the support. These will be stabilized and fixed.


Picture 3 is the battery tray after A LOT of pounding and welding. I still have a few pinholes to fix here.


Picture 5 is another shot of the sliced grille support. It will be re-welded after reshaping the opening is complete.


Pictures 7 and 8 show the commission plate and the two body number plates. I found the upper body number plate interesting...especially the low number, 51. Any idea if this plate was fitted to special order cars like this one?
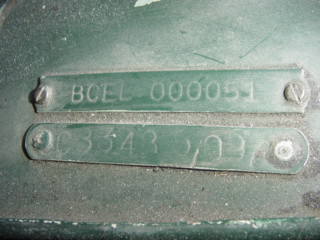
Hope you've enjoyed the latest look...I hope to get back to the car in a few weeks!
Finally, a little progress!

I can't say there's a lot that's been going on with the estate lately. Between my new job and a lot of sickness in the family, plus the holidays, there just hasn't been a lot of time. I did find about four hours to work on the car between Christmas and New Years, though. After finding out that the "new" nose that had been put on the car was installed over some...less than pristine (diplomatic enough?) bodywork, I kept going. Managed to weld up most holes, still have a little to go, bent the battery tray and radiator support panel back into shape, and did the rough reshaping of the grille opening necessary to fit the grille back in! Apparently, it was a better idea at the time to flatten the grille instead of making sure the opening was the stock height. Consequently, I've used a scissors jack and some planks to jack the opening back to it's correct height (!). The pictures tell the story...
Subscribe to:
Posts (Atom)